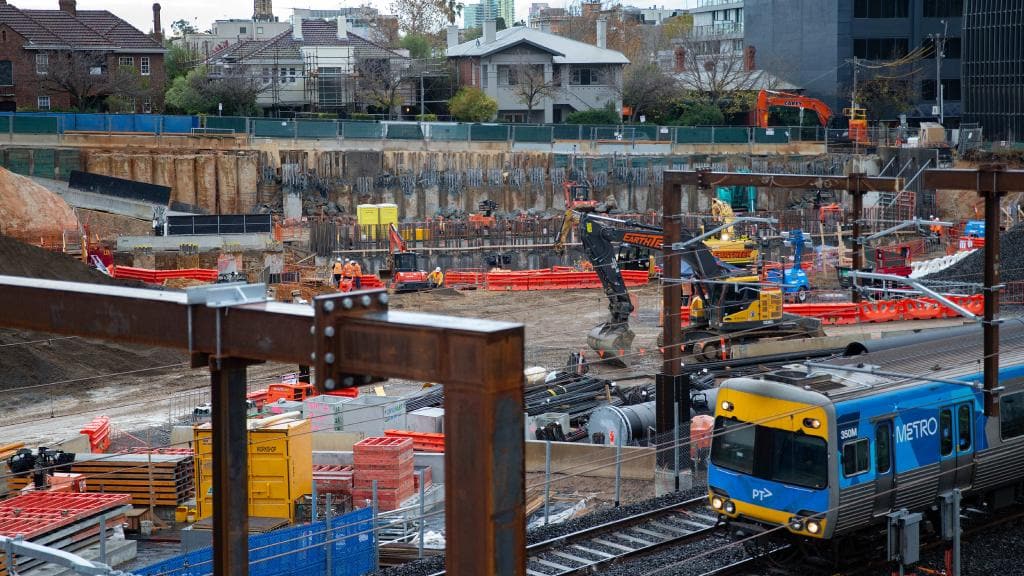
According to reports from Fairfax Media today, the Labor government will announce a $9 billion grant for the Melbourne Metro Tunnel. In addition, the Labour government has invested 40 million Australian dollars to make the project “ready.”
Before the shovel digging the ground, the railway tunnel is facing a series of engineering challenges. According to reports, these measures include deciding whether to run new tunnels under or above existing urban loops, the beginning of construction work at the Victoria Integrated Cancer Center, and the presence of aquifers under and along the Yarra River. The proposed tunnel will be there to run. The former Victorian government announced the project in 2009, including a 9-kilometer tunnel connecting South Kensington and South Yarra, and five new subway stations, which will eventually transport 60,000 passengers per hour. The tunnel project in the Melbourne area told us that it is not easy to build all the tunnels. But the good news is that there are many global examples that prove that this type of construction can be carried out safely. While not wishing to participate in the proposed tunneling technique rather than the other, it is necessary to study some technical issues and the best practices of underground tunnels in cities such as Melbourne.
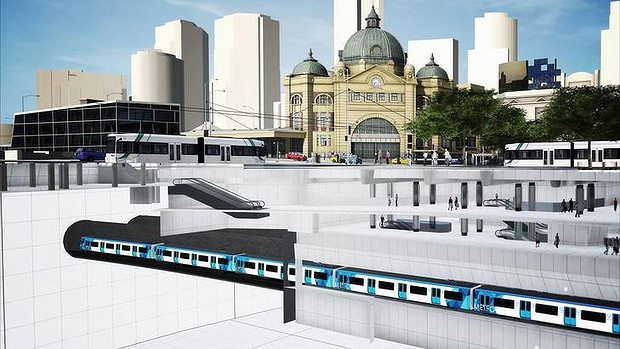
Ground excavation
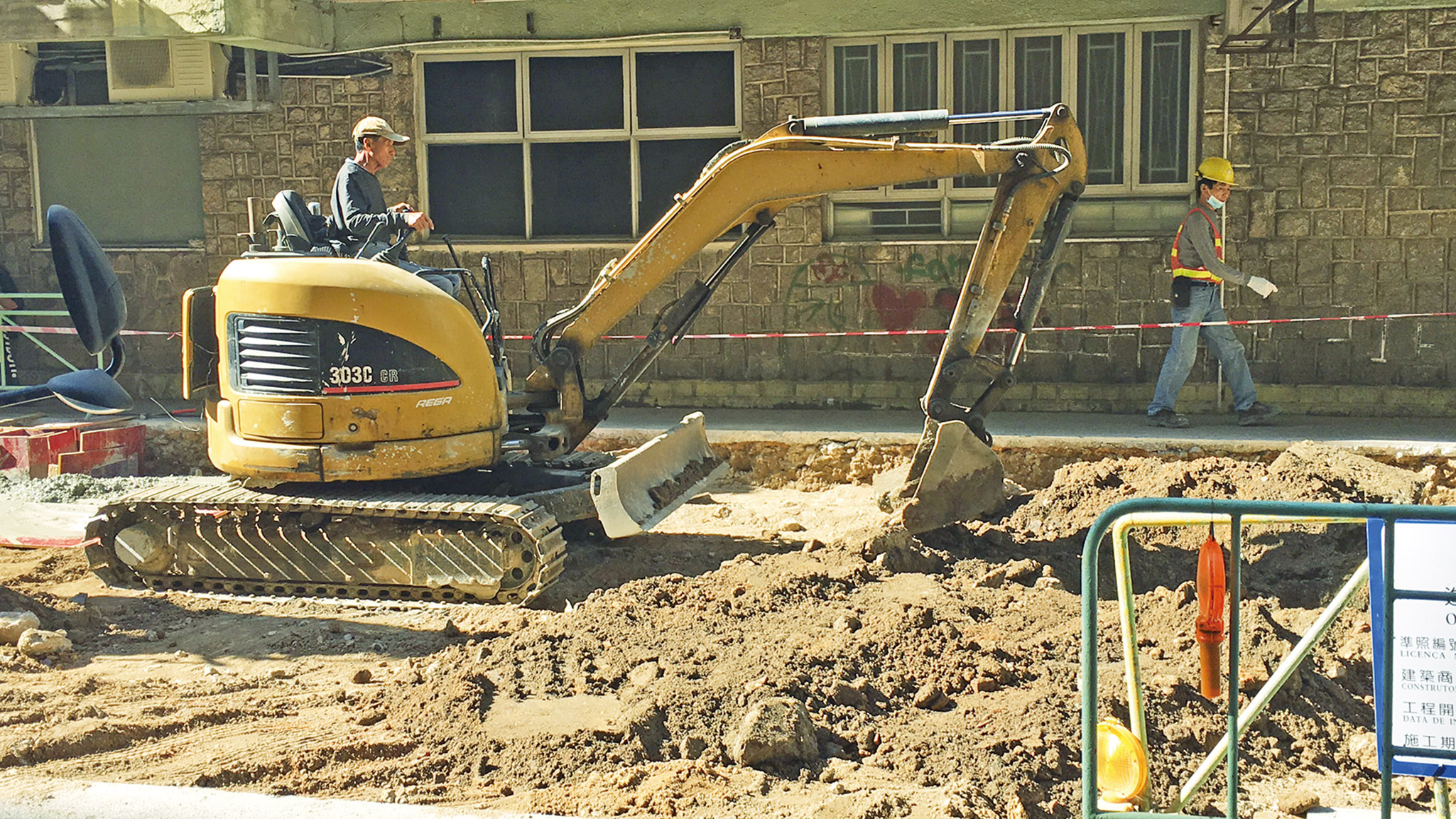
The study of any deep foundation pit begins with a clear understanding of the geology that must be “breakthrough” and the water level connected to the site. Adjacent water sources, such as rivers or aquifers, may be supplied by wells dozens of kilometers away, and need to be explained. Detailed soil profiles are critical to the final design, based on future soil samples along the tunnel and nearby. Prior to the establishment of these projects, the geological maps and reports of previous projects in the area were extremely valuable. For the Melbourne Metro Tunnel project, the initial source of information was the Melbourne SJ 55-5 geological map published by the Victorian Department of Primary Industries. Unsurprisingly, this map is consistent with the observations of engineers involved in the construction of the Burnley Tunnel between 1996 and 2000. They reported that a layer of weathered basalt was on top of a thick layer of silt and clay.
The shaft leading to the tunnel must be dug through a 20-meter-thick gravel aquifer, the gravel gravel layer on Mali Street. At the bottom of the aquifer, the bedrock is like a flat bowl, made up of dark marine sediments called Melbourne mudstones (made up of silt and sand). Since the mudstone is porous, the water in the aquifer can leak deeper and engulf the pipes of the Burnley Tunnel, so it must be made waterproof. In addition, the tunnel walls need to be designed to be strong enough to withstand the hydrostatic pressure from all sides (the pressure exerted by the stationary liquid). Of course, these different soil types are not well aligned: they are folded up, entangled like an extruded tablecloth, mixed with small to large stones. Finally, the surface layer is usually composed of topsoil, which may be from previous artificial fillers. Based on the information from these two sources of cooperation, we can conclude that the proposed Melbourne subway tunnel must be dug below the water table, through different amounts of alluvial, oceanic and weathered volcanic material considered to be “soft” ground.
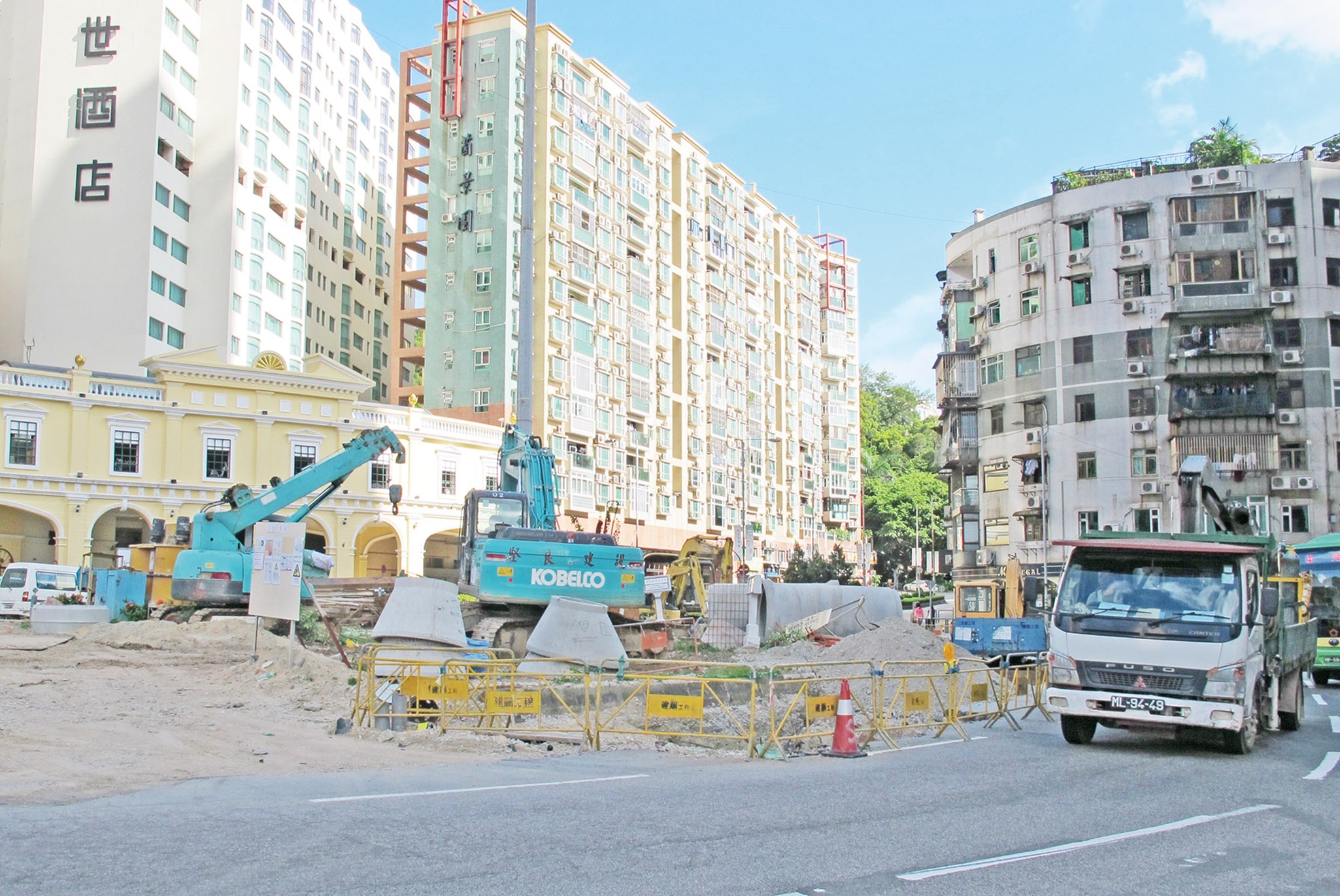
Softening project
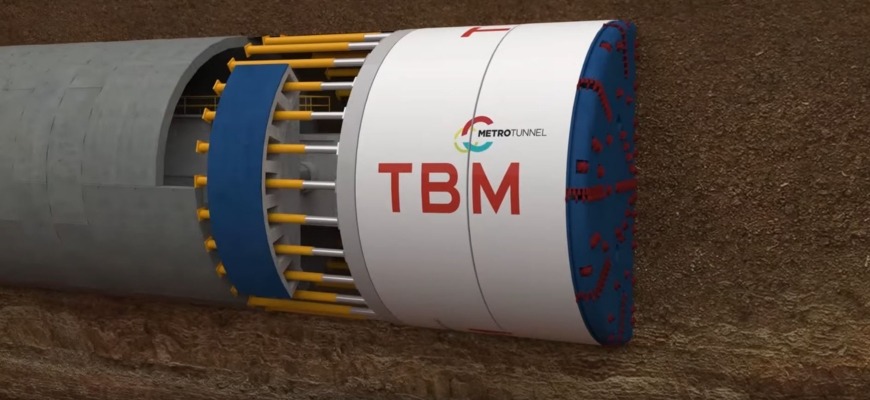
The tunnel boring machines (TBMs) were built by American engineer James Robbins in the 1950s. They were designed to drill through the hard rock made of granite, and the speed is based on the method of drilling and blasting. 10 times. This record has been broken many times and the number of accidents has dropped. For example, the new tunnel, which crosses the Swiss Alps, is 57 kilometers long and is the longest tunnel in the world.
Because soft ground tunnels cannot use the “soft” wall to push themselves forward, a different “foundation” is needed. A simple solution is to install a tunnel wall made of sturdy precast concrete members behind the tunnel. Most of the world’s largest cities are built on soft soil because they evolved from ancient trade villages near lakes or major rivers. As the population expands, people need larger sewers and drainage pipes, and recently they need to build subways and highways underground. The softness of the soil creates a special TBM called the Earth Pressure Balance (EPB) shield or machine.
We should not be surprised that 50% of EPB tunnels are built below the water table. Major cities using EPB shields include Shanghai, Bangkok, Rome, Naples, Barcelona, Madrid, Rio de Janeiro, Los Angeles and London. The key risk of soft underground engineering is soil subsidence above the tunnel, which is caused by soil rearrangement caused by tunnel construction. Not surprisingly, the main goal of a geotechnical engineer is to ensure that it is balanced so that it does not damage the surface structure. Recent advances have made this job easier: in fact, in the past 10-15 years, EPB shielding technology has added important features. Helping these very important enhancements is better computer models for predicting soil behavior under buildings; pre-tunnelling in situ testing; high-difficult subsurface grouting pretreatment or grouting; new materials; and of course, from the world A great deal of knowledge gained from successful projects around the world.
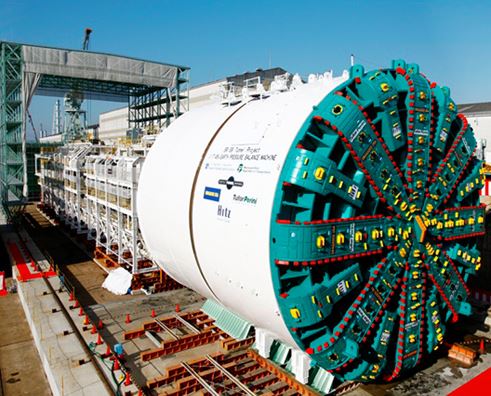
Perfect for the future
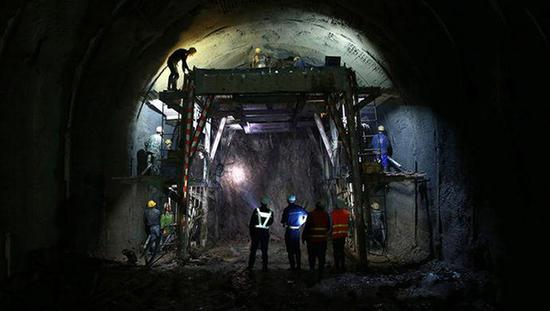
The old subways in Toronto, New York, and Boston are usually built under the sidewalks of the main roads, using the so-called “digging roads” method. As the term implies, the building may cover the large opening with beams and steel plates, starting from cutting an initial space. The excavation is pushed down while the traffic is directed around the necessary openings to reduce or enhance the material.
Of course, construction-related trucks, cranes, and concrete mixing opportunities disrupt pedestrian and vehicular traffic along the tunnel. Social and corporate pressures have led to the elimination of the often cheaper cutting and covering methods, which have been replaced by the use of “deep holes” in the drill.
As mentioned earlier, as part of the Melbourne Metro project, five new stations will be built, and these challenges are not related to the tunnel. The space station not only needs extra space but also needs to be connected to the ground. The underground passage to the adjacent shopping mall or office building is also a very attractive addition. The circular trampoline is not used to build a station. At the same time as the digging method, the station can also be built from the bottom up using the New Austrian Tunneling Method (NATM). The basic premise of the new Austrian law is to create a solid roof and side walls before using large equipment to dig underneath the casing. The new Austrian law is not only suitable for the cross tunnel between the station and the two tunnels, but also can be combined with the “cousin” of the digging method to create a construction method that is up and down, that is, the load-bearing wall and the column are first drilled from the top.
The next step is to build up the visible portion of the station, while digging underground (using the new Austrian method from the tunnel up, or down) to remove a large amount of excavated material through the existing tunnel portion previously drilled by epb-shield. This will not only eliminate the need for large dump trucks on the ground, but will also speed up construction.
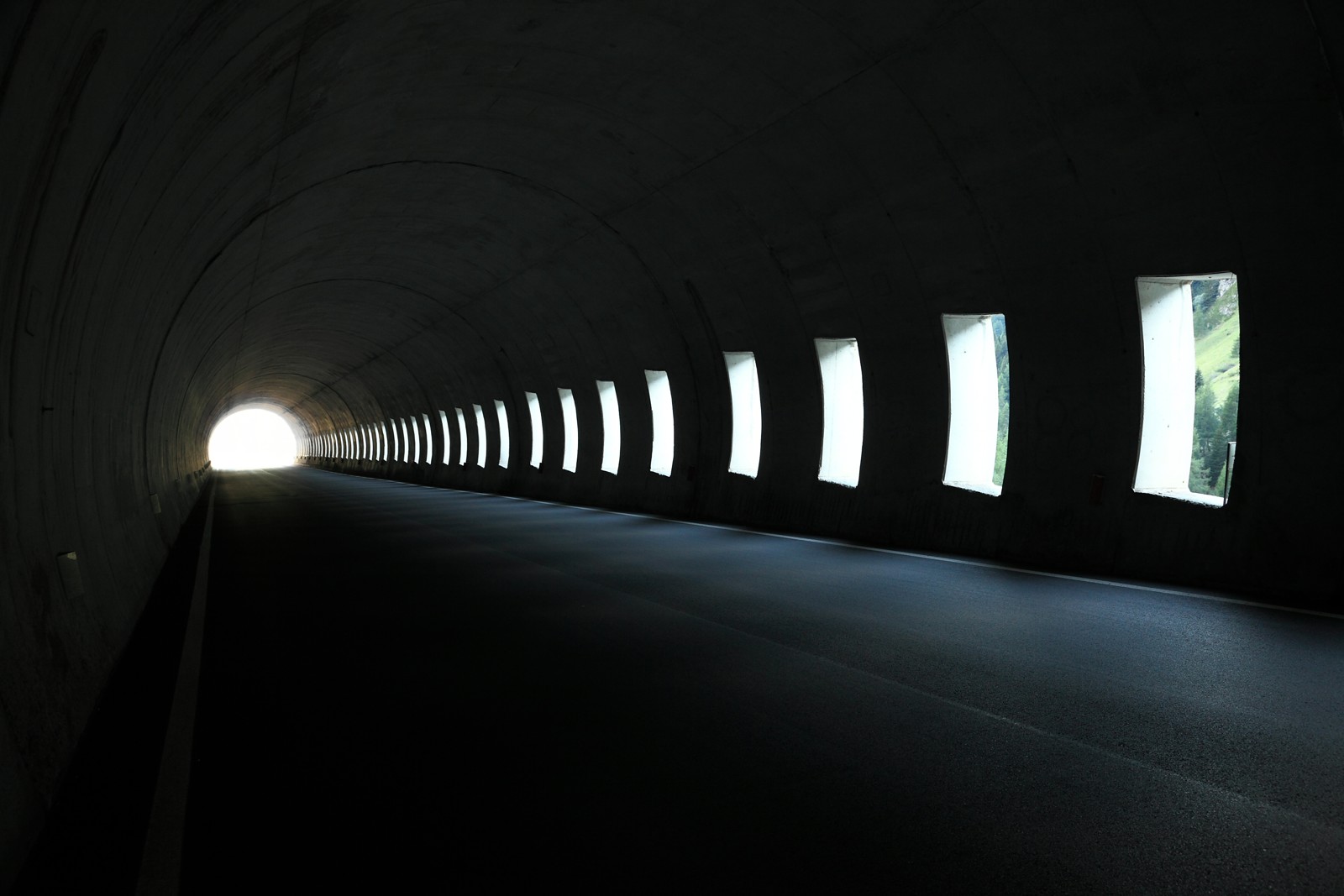
Bright at the end of the tunnel
The best solution for the Melbourne Metro Tunnel requires close collaboration with all stakeholders, and tunnel engineers and contractors provide expert advice on state-of-the-art tunnel technology. Regardless of which route you choose, EPB Shield technology seems to be the safest, most efficient, and most economical alternative to building a pipeline through Melbourne’s soft, “water-filled” underground. In order to minimize the impact of large trucks on the station excavation in the city, it seems that the “up and down” construction combined with the new Austrian law, through advanced grout protection, and through the tunnel to remove silt, will provide the most ideal solution. The politics of the project (currently close to the top of the national priority list for Australian infrastructure) will continue to be fascinating; but technical challenges and solutions to these challenges will continue to move forward.
In the near future, will you still expect to board the newly opened Melbourne Metro train? Probably not. In many cases, when it comes to building such large projects underground, we have to anticipate delays mainly caused by geological factors.
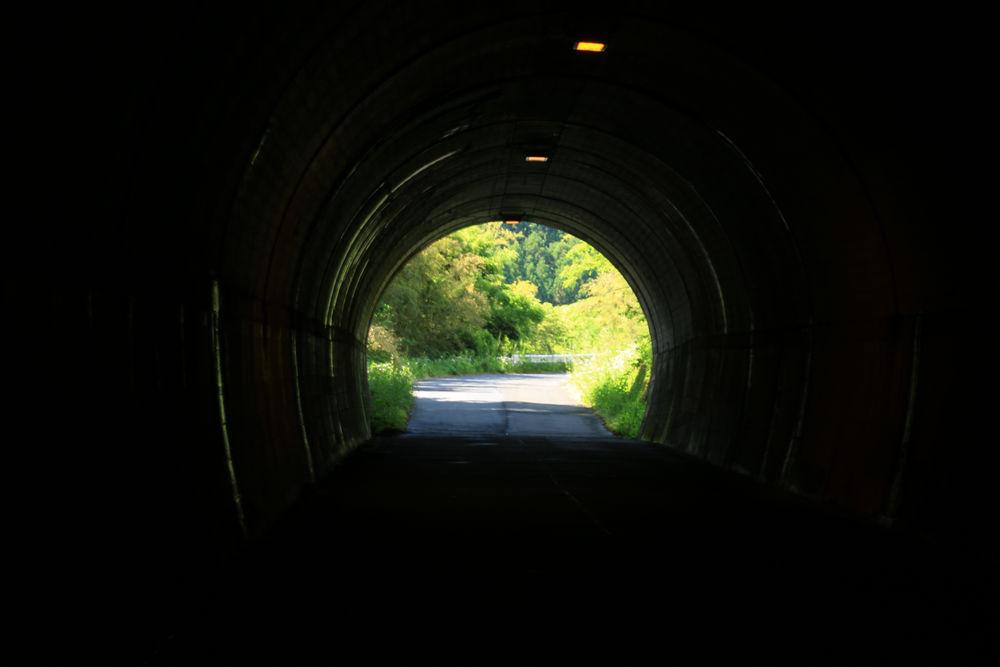
Https://theconversation.com/dig-this-how-to-construct-melbournes-metro-tunnel-safely-12588