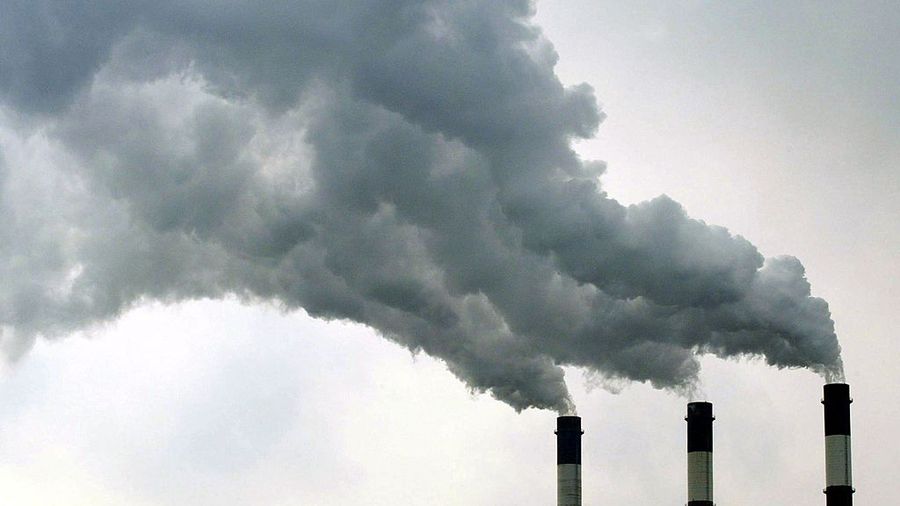
There may be no chimneys that can be seen, but whenever we set up a poorly designed structure or use energy-intensive solutions to cool, heat and operate inefficient buildings, we push the greenhouse gas emissions curve. In Australia, our built environment currently represents a huge “carbon debt”.
Our mission is to reverse this trend. We are reimagining the way buildings are conceived and produced. We want to produce carbon-positive building products and build evidence bases to transform our cities through thoughtful policies and planning innovations. We plan to cut emissions by about 10 million tons a year, and we have seven years of federal government funding to do this.
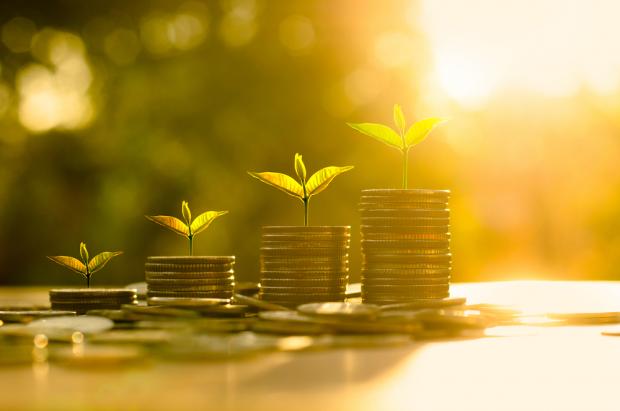
Building concrete and steel are a fashion
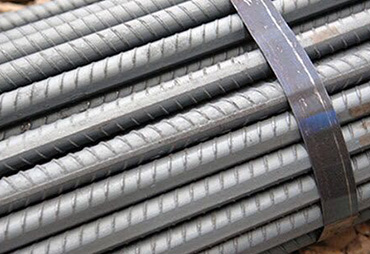
This seems too optimistic. Since the global community began to seriously worry about global warming, national emissions have been steadily rising, and our team is looking for all these savings in only one major department; the buildings around us. Since 1990, Australia’s emissions have increased from 418 million tons to 545 million tons (2009) or more than 30%. But we believe that deep, meaningful emissions reductions can be achieved without compromising our standard of living.
Building a house has greatly increased our emissions. The electricity consumption of houses and apartments accounts for about 16.5% of Australia’s emissions. There is also “reflected” energy in the production and processing of building materials. For each ton of concrete and cement, approximately equivalent amounts of greenhouse gases are emitted. This accounts for about 10% of global emissions. Steel production is close behind. This is the two materials at the heart of modern building technology.
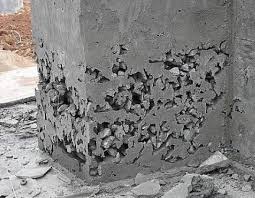
Simple design changes can make a lot of difference
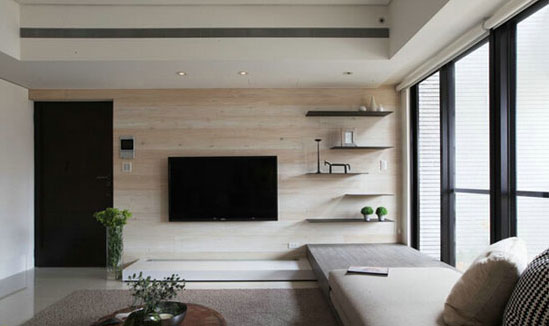
But change does not necessarily mean changing the clock (although it is helpful to rediscover the use and aesthetics of natural renewable materials). Instead, we are looking for ways to integrate solutions into our daily lives, rather than trying to apply solutions to our unfavorable world. One way is to take the roof of Australia. We should integrate the solar panels into the roof slab so that the time the roof is on the building begins to repay its carbon liabilities by inputting electricity to the grid. The same is true for cladding systems that absorb energy and convert it into energy.
Using these products as standard devices, rather than afterwards, is a simple and easy way to incorporate deep, meaningful emissions reductions into the structure of our city. Improving materials can also help. We are also working to reduce the carbon footprint of cement and concrete. Recycling fine fly ash waste from coal-fired power plants and using it to replace most of the carbon in concrete can reduce emissions. Materials scientists at the University of New South Wales have obtained patented and commercial green steelmaking processes. It reduces emissions by up to 16%; instead of burning coke in an electric arc furnace to power the system, it uses waste plastics and used tires.
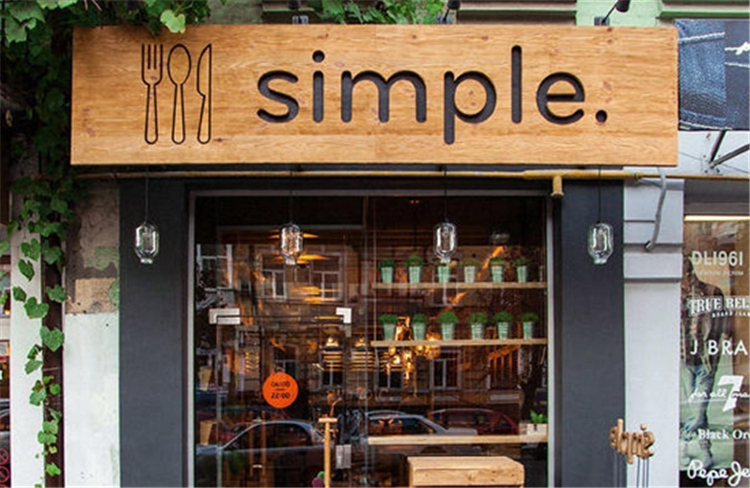
Cost reduction curve
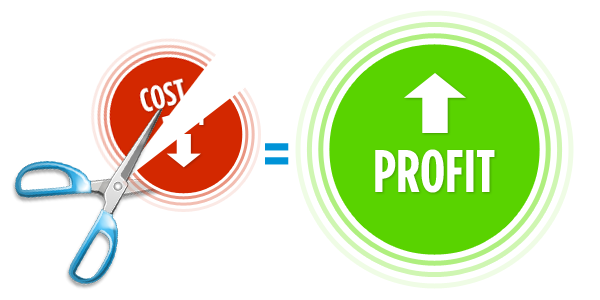
But what about the large number of buildings we have? Many of these designs are not suitable for the Australian climate and require ever-increasing cooling and heat. One of our research briefs provides evidence-based answers to some of the social and psychological issues surrounding why we live outside the environment. For example, why do people make so many “abnormal choices”? Why do they buy a cheap new home, even if it devours energy because of short-sighted design, so long-term residence will be more expensive? Is there a simple answer, such as redesigning financial products to encourage people to spend more wisely? The bottom line of change is affordability. Environmentally friendly products will never be “mainstreamed” unless they can compete on price. Solar panels are a good example. Mass production means that prices have fallen sharply, and today it is possible to buy a 1.5 kW system for $4,000. As electricity prices rise, it will recover costs within a few years.
The maximum life cycle cost of an office building is the wages of workers, so green buildings can significantly increase worker productivity by 1-5% (in different case studies) to bring significant advantages to tenants. In many cases, increased construction costs can be restored in two to three years. The CRC is interested in the evidence base of high-performance buildings, so it is better to understand the lease discussion. It is interested in the “closed loop” of environmental, social and economic factors, so designers can use this knowledge to provide “measurable better buildings”. The key now is to join the point of connecting all the great innovations already on the market, or wait. If we figure out how to combine good ideas and then connect them to our real world market, we can achieve our goal: by 2027, we can save 30 million tons per year from the Australian built environment alone. The amount of emissions.
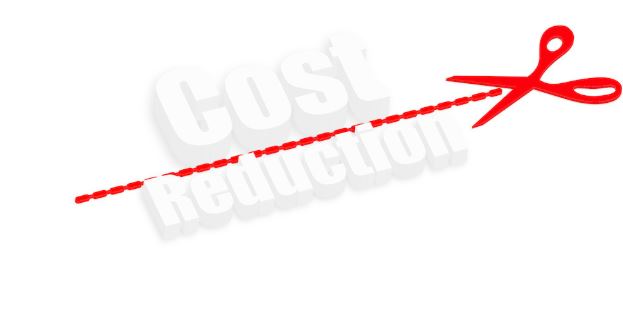
Https://theconversation.com/intelligent-design-time-to-wise-up-and-build-for-the-climate-5424